Газобетонные изделия в строительстве получают «второе рождение» ввиду повышения норм теплоизоляции зданий и удорожания энергоносителей. Немногие предприятия поточно производят продукцию, сохраняя стабильно высокое заявленное качество на уровне лучших природных материалов, например, древесины и камня. Газоблоки грас — это реализация инновационных немецкой и нидерландской технологий WEHRHAHN и HESS AAC Systems B.V. соответственно. Изделия сочетают требуемые практикой строительства эксплуатационные, технологические характеристики по критерию цена-качество.
Достоинства
Газобетонные блоки — уникальный материал, объем которого до 85% — воздух, запечатанный сферы. Газоблоки имеют анизотропные свойства благодаря равномерному распределению пустот. Уникальный набор свойств блоков грас сочетает низкую теплопроводность и высокую паропроницаемость (на уровне дерева), высокую прочность (сравнимую с природным камнем). Долговечность применения — десятки лет (больше 55 лет). Большие габариты, небольшой вес изделий позволяют сокращать сроки и трудоемкость работ, а значит — финансовые траты.
Материал по составу экологичный и биохимически нейтральный. Камень легко принимает любую форму, а небольшой вес кладки удешевляет фундамент. Сочетание высокой пожароустойчивости и морозостойкости расширяет географию применения газоблоков. Кладка стен обеспечивает хорошую звуко- и шумоизоляцию. Блоки грас имеют абсолютно идентичные форму и габариты.
Вернуться к оглавлениюЛегкость
Относительно небольшая масса газосиликатных блоков позволяет зданию опираться на облегченный фундамент. К примеру, камень плотностью D500 с габаритами 625х250х400 мм весит 30,5 кг, а фрагмент кирпичной кладки с аналогичными характеристиками теплопроводности и объемом имеет массу 120 кг (25 шт. кирпича). В первом случае толщина стены 400 мм, а во втором — уже 640 мм. Легкость камня упрощает грузоподъемные работы и транспортировку продукции (масса 1 м3 газоблоков 400 – 700 кг). Стены и перегородки возводятся быстрее, причем и в многоэтажных зданиях.
Экологичность
Материал не содержит токсичных компонентов, а по свойствам природной естественности уступает лишь древесине. Вместе с тем камень не является пищей для грызунов, в нем не образуются плесень и грибки. Радиационный фон продукции не превышает 10 мкР/час.
Пористая структура газобетона поддерживает комфортную температурно-влажностную среду (как в деревянном доме). Производство имеет отходы, которые вторично используются для изготовления камня. Высокая температура и давление автоклавного твердения обеспечивают биологическую чистоту материала.
Вернуться к оглавлениюЭкономичность
Простые доступные компоненты и автоматизация процессов снижают стоимость газобетонных блоков. Расход электроэнергии на производство 1м3 автоклавных газоблоков грас в 2 – 3 раза меньше, чем на изготовление кирпича. Крупные газоблоки легче, поэтому удешевляются фундаменты, и ускоряется возведение стен. Точность изготовления позволяет формировать тонкие кладочные клеевые швы (до 5 мм).
— Регулярная проверка качества ссылок по более чем 100 показателям и ежедневный пересчет показателей качества проекта.
— Все известные форматы ссылок: арендные ссылки, вечные ссылки, публикации (упоминания, мнения, отзывы, статьи, пресс-релизы).
— SeoHammer покажет, где рост или падение, а также запросы, на которые нужно обратить внимание.
SeoHammer еще предоставляет технологию Буст, она ускоряет продвижение в десятки раз, а первые результаты появляются уже в течение первых 7 дней. Зарегистрироваться и Начать продвижение
Поэтому эксплуатационные затраты на обогрев и охлаждение зданий сокращаются. Доставка блоков на объект, подъем на высоту стоят дешевле по сравнению с аналогичными материалами. Возведение 1 м2 стены из кирпича стоит примерно в 4,3 раза дороже, а деревянной — в 2 раза дороже, чем из газоблоков.
Вернуться к оглавлениюТеплопроводность
Изделия с плотностью D500, D600 (конструкционно-теплоизоляционные) могут использоваться в наружной кладке жилья, общественных построек без дополнительного утепления. Величина коэффициента теплопроводности такой продукции в реальных условиях находится в пределах 0,14 Вт/(м °С), что соответствует дереву. К примеру, для обеспечения такой низкой теплопроводности кирпичная стена должна будет иметь толщину 1,2 м.
Вернуться к оглавлениюЭнергосбережение
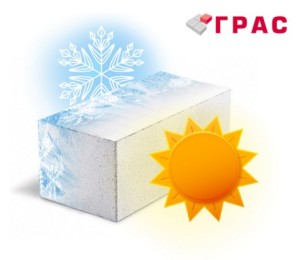
Газобетонный блок обеспечивает нормативную энергоэффективность зданий, которую определяют величина накопленного тепла и отношение времени остывания камня к аккумулированному его объемом теплу. Стены из дерева и газоблоков теряют температуру примерно с одинаковой скоростью, а вот кирпич (пустотелый и полнотелый) остывает соответственно в 3 и 4,8 раза быстрее. Задача эффективной экономии тепловых ресурсов при сохранении комфортной температуры решается возведением стен из газобетона плотностью 400 – 500 кг/м3. Уплотнение материала увеличивает прочность, но ухудшает теплоизоляционные свойства. Продукция с плотностью 700 кг/м3 теряет 50% теплоизоляционных свойств.
Вернуться к оглавлениюЗвукоизоляция
Комфортность пребывания в помещениях также определяется степенью тишины. Крошечные воздушные пустоты в материале создают структуру, способствующую затуханию любых звуков и шумов. Ее эффективность в 10 раз выше, чем у кирпичной кладки. Воздушные полости между слоями газоблоков или отделка стен материалами большей плотности может обеспечить шумоизоляцию на уровне 45 – 50 Дб.
Вернуться к оглавлениюПожаробезопасность
Составляющие материала газоблоков грас негорючи. К примеру, норматив огнестойкости для плит перекрытий REI 60 (СНиП 21-01) — сохранение несущей способности при пожаре в течение 60 мин. В реальных испытаниях 6-ти метровая плита плотностью D600 под нагрузкой 300 кг/м2 сохранила характеристики под прямым воздействием огня продолжительностью 70 мин. Перегородки с плотностью D400 – D600 шириной 75 (100) мм подтвердили сопротивление огню в течение нормативного интервала времени в 3 часа (соответствие типу I противопожарных преград, пределу огнестойкости RЕI180). У газобетонного блока высший класс пожаробезопасности — «К0».
— Разгрузит мастера, специалиста или компанию;
— Позволит гибко управлять расписанием и загрузкой;
— Разошлет оповещения о новых услугах или акциях;
— Позволит принять оплату на карту/кошелек/счет;
— Позволит записываться на групповые и персональные посещения;
— Поможет получить от клиента отзывы о визите к вам;
— Включает в себя сервис чаевых.
Для новых пользователей первый месяц бесплатно. Зарегистрироваться в сервисе
Прочность
Классы прочности камня на сжатие определяются технологией производства, а не плотностью материала. Достигнутый уровень — это выпуск сертифицированных (требования ГОСТ 31360-2007) газоблоков грас класса D600 с повышенной прочностью В5,0 (100 кг/см2). Из них возможно возводить самонесущие стены высотой до 20 м. Так, камень с габаритами 625х300х250 мм в пересчете выдерживает нагрузку больше 180 т. Теплоизоляционные блоки от D200 до D350 соответствуют классам от В0,35 до В2,5, конструкционно-теплоизоляционные изделия от D400 до D500 — от В1 до В2,5. Последнее значение позволяет из таких блоков возводить несущие стены зданий до 3-х этажей, В2 — в постройках до 2-х этажей, В3,5 (50 кг/ см2) — в 5-ти этажных зданиях.
Вернуться к оглавлениюТочность
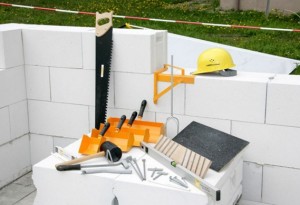
Технология позволяет иметь отклонение геометрических размеров камня в пределах 1 мм (включая конструкцию гребень – паз). Поэтому при соблюдении правил кладки стенам не требуется существенное выравнивание поверхности, объемы отделочных работ сокращаются. Достаточно нанести шпатлевку и окрасить. Стены, образованные прямоугольными и U-образными блоками, обладают точной геометрией.
Вернуться к оглавлениюГигроскопичность
Микропустотная структура материала не является гигроскопичной (не сосет воду), ввиду замкнутости воздуха в многочисленные сферы. Газоблоки быстро возвращают в воздух влагу осадков без изменения габаритов. Вместе с тем материал дышит как древесина, удаляя из воздуха помещений избыточную влагу, газы, и пропуская в обратную сторону отрицательные ионы кислорода.
Значение паропроницаемости камня D500 в четыре раза лучше, чем у сосны. Показатели равновесной влажности массы камня в стенах — 4 – 5% к его массе. Аналогичная характеристика дерева — выше в 4 раза (древесина дольше сохнет). Замерзшая в массе изделий влага не разрушает и не деформирует их, так как льду достаточно внутреннего пространства для расширения.
Вернуться к оглавлениюОбласти применения
Задачи строительства по месту и целям обеспечиваются автоклавными газоблоками со специальными характеристиками. Это формирование несущих стен зданий высотой до 20 м (камень D600 класса В5,0), возведение перегородок, формирование армопоясов, заполнение каркасов высотных строений, производство плит перекрытий. Материал используется для наращивания этажности построек, теплоизоляции наружных стен, обустройства дымоходов, вентиляционных и лифтовых шахт, формирования противопожарных брандмауэров.
Вернуться к оглавлениюКак изготавливаются
Литье высококачественных газоблоков грас — автоматизированное производство на импортных линиях. Сырье проходит проверку и выбраковку. Компоненты: портландцемент (известь), кварцевый песок, гипс, вода и алюминиевая паста (газообразователь). Тщательно перемешанная смесь разливается в формы, подвергается высокочастотной виброобработке и предварительно твердеет несколько часов в специальной камере.
Набравшую прочность массу разрезают на блоки, но не разделяют и отправляют в автоклав (12 часов при давлении 12 бар и температуре до 190 град.) на пропаривание. В нем создается уникальная прочная ячеистая структура материала, на 85% состоящая из пустот. Затем массив разделяется на отдельные изделия и после упаковывания готов к использованию.